Stuttgart / October 08, 2024 - October 09, 2024
Hy-fcell
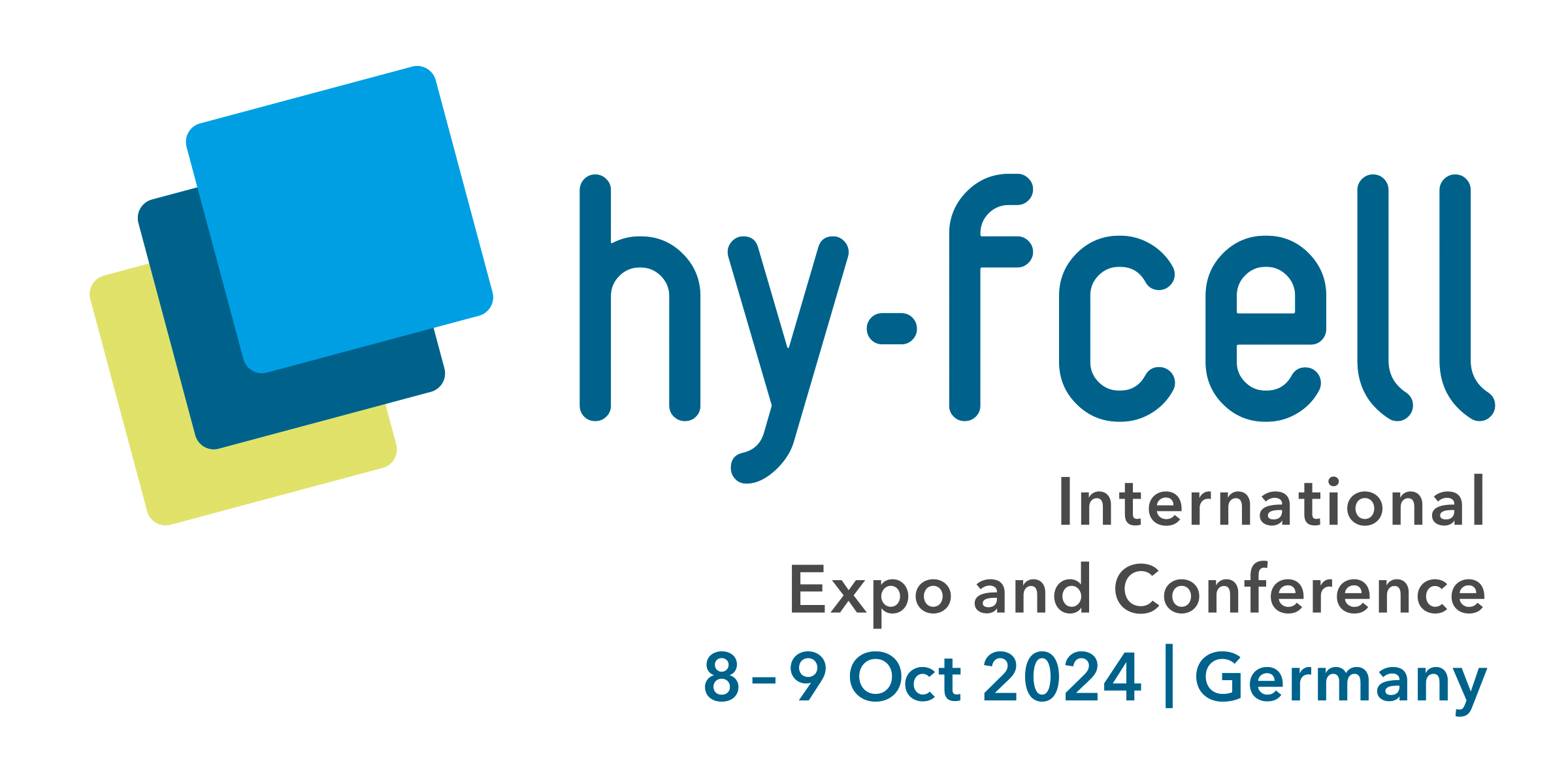
hy-fcell is a leading international trade fair and conference for hydrogen and fuel cell technology. The trade fair is a key meeting place for the industry and offers both experts and newcomers the ideal platform to discuss technological advances, transfer knowledge and open up international markets.
We look forward to presenting a wide range of exhibits from our technology areas "Surface Technology" and "Cutting & Joining" at Hy-fcell in Stuttgart in Hall 4, booth 4E51.
The bipolar plate is the central component of the fuel cell. It controls the supply and separation of the reaction gases, integrates cooling channels to remove the reaction heat and establishes the electrical contact between the anode and cathode. Bipolar plates are usually made of metal or composite materials. Currently, the susceptibility to corrosion of metallic bipolar plates and the manufacturing resistances of composite materials limit their use on a large scale.
The structuring of bipolar plates using laser radiation is a key technology for fully exploiting the potential of fuel cells. Laser processing creates surface structures that facilitate the removal of corrosive reaction products, improve flow properties and reduce electrical resistance
New processes enable large-area, continuous processing on a 5-axis system with femtosecond lasers. This allows the surface energies of metallic bipolar plates to be specifically adjusted and the resistances of composite plates to be precisely investigated.
In the course of the energy transition, the demand for technologies such as PEM fuel cells is constantly increasing. The Fraunhofer ILT is developing a laser-based process that enables the production of innovative corrosion protection coatings for bipolar plates (BPP). In this process, a precursor is sprayed onto the BPP and dried. The subsequent functionalization using laser radiation converts this precursor layer into a conductive and corrosion-resistant coating.
The process dispenses with complex and expensive vacuum processes, making it considerably easier to use in a continuous production line. The short interaction time between the laser beam and the workpiece minimises the thermal load on the latter.
Double beam welding speeds up the production of bipolar plates (BPP) by almost 50 percent by using two laser beams simultaneously. This increases the welding speed, improves the seam quality and avoids typical defects such as humping. This makes production more efficient and better able to meet the requirements of hydrogen technology.
Another important approach is to extend the service life of forming tools that are subject to heavy wear due to mechanical stress. Extreme high-speed laser cladding (EHLA) is used to apply wear-resistant coatings to low-cost structural steels, which significantly extends the service life of the tools. This process also enables tools to be repaired, which reduces production costs and increases sustainability. These innovations make production faster, more cost-effective and more sustainable, which makes an important contribution to the further development of hydrogen technology.
Would you like more information about our innovations relating to our hydrogen technologies?
Join the hydrogen laboratory at Fraunhofer ILT now in our 360 ° - tour