Hannover / March 31, 2025 - April 04, 2025
Hannover Messe 2025
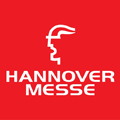
We look forward to showcasing a wide range of exhibits on various topics at our booth at the Hannover Messe.
In the AI-SLAM project, Fraunhofer ILT has developed an innovative AI-powered solution to efficiently and resource-consciously repair heavily used mining tools such as excavator buckets, chisels, or rock crushers. Instead of replacing worn-out components, the institute relies on Laser Metal Deposition (LMD). In this process, a metal powder is locally melted using a laser beam and applied layer by layer until the original contour is restored. For additional hardness, stainless steel is applied at 1300°C and simultaneously reinforced with tungsten carbide particles. As the material cools, these particles form an extremely durable protective layer against wear and corrosion.
The main challenge lay in optimally coordinating over 150 process parameters, such as the mixture of steel and carbide, laser power, or toolpath guidance. Too many carbide particles make the coating brittle, while too much stainless steel reduces hardness.
This is where Artificial Intelligence comes into play: The experts at Fraunhofer ILT developed a multi-stage AI system that fully automates the repair process. A line laser with a CMOS camera first captures the worn-out contour of the tool and compares it to the original shape. The AI then calculates the layer thickness and deposition pattern. During coating, a camera system detects deviations in real time and adjusts the parameters accordingly. The AI module was integrated into the OpenARMS operating software from project partner BCT.
Automation makes the repair process significantly faster, more precise, and reduces the workload for operators. Project partners include the National Research Council Canada, McGill University, and AI specialist Braintoy.
Given the increasing demands on pipelines for transporting next-generation energy carriers such as hydrogen, ammonia, and liquefied natural gas, the need for high-alloy materials is growing. However, constructing kilometers of pipelines from these expensive materials presents a significant financial and resource-related challenge for the expansion of Europe's energy infrastructure.
The Fraunhofer Institute for Laser Technology ILT has developed Extreme High-Speed Laser Material Deposition (EHLA) to address these challenges. Using EHLA, the inner diameter of pipes can be coated with a thin metallic protective layer, allowing the use of cost-effective, low-alloy base materials. This economically attractive coating provides corrosion protection, increases wear resistance, and prevents hydrogen embrittlement. Additionally, the process enables the retrofitting of existing pipelines, adapting the infrastructure to meet the requirements of sustainable energy carriers.
At Hannover Messe 2025, Fraunhofer ILT will showcase EHLA technology with a special exhibit: a cross-sectioned, internally coated pipe along with the specially developed EHLA processing optics will be presented as a demonstrator. Visitors will have the opportunity to experience the technology and its functionality firsthand. Digital content on accompanying monitors will provide additional insights into the applications of EHLA internal coating.
The key advantage of EHLA technology lies in the cost-efficient and resource-saving production of pipelines. Beyond hydrogen transport, this solution is also well-suited for the chemical and food industries, where it can replace solid-material pipes, reducing costs and conserving resources. Furthermore, the coating extends the lifespan of existing pipelines or enables their adaptation to new applications.
The combination process Simultaneous Machining and Coating (SMaC) developed at the Fraunhofer ILT enables the combination of the EHLA coating process with a subtractive finishing step in parallel with the main production time, thus increasing productivity enormously. In addition to the economic advantages, the SMaC process also offers technological benefits compared to the conventional process chain. The process heat generated in the coating process leads to a softening of the material and thus to easier machining. This makes it possible to produce corrosion and wear protection coatings as well as functional surfaces more quickly and with less wear on the tools. SMaC technology offers considerable advantages, particularly when applying high-strength coating materials that are otherwise difficult to machine.
Ensuring competitiveness in manufacturing companies requires continuous improvements in component specifications or cost-efficient process chains for production and circular economy strategies. An innovation in this field is Extreme High-Speed Laser Material Deposition (EHLA). This modified laser cladding process significantly increases coating efficiency for wear and corrosion protection by enabling high feed rates (> 20 m/min) and the processing of difficult-to-weld materials. Originally developed for rotationally symmetric components, Fraunhofer ILT has adapted the process for 3D applications (EHLA3D). This advancement enables additive manufacturing, freeform surface coating, and repairs of non-rotationally symmetric components while maintaining high deposition rates and fine structural resolution.
Thanks to precise heat input, EHLA3D can produce thin-walled structures with wall thicknesses of less than 1 mm as well as massive volumes, crack-free and with relative densities above 99.5%—all at high productivity. These properties allow for the flexible production of lightweight components, such as those made from difficult-to-weld aluminum alloys. This capability is demonstrated in an exhibit featuring an aluminum flange with variable overhang geometries, built in less than an hour.
The advantages of EHLA3D lie in the fabrication of delicate, thin-walled components, the processing of advanced materials, and near-net-shape manufacturing. This opens up new industrial applications, such as:
EHLA3D thus contributes to material savings, functional optimization, and sustainable resource utilization.