Frankfurt / November 19, 2024 - November 22, 2024
Formnext 2024
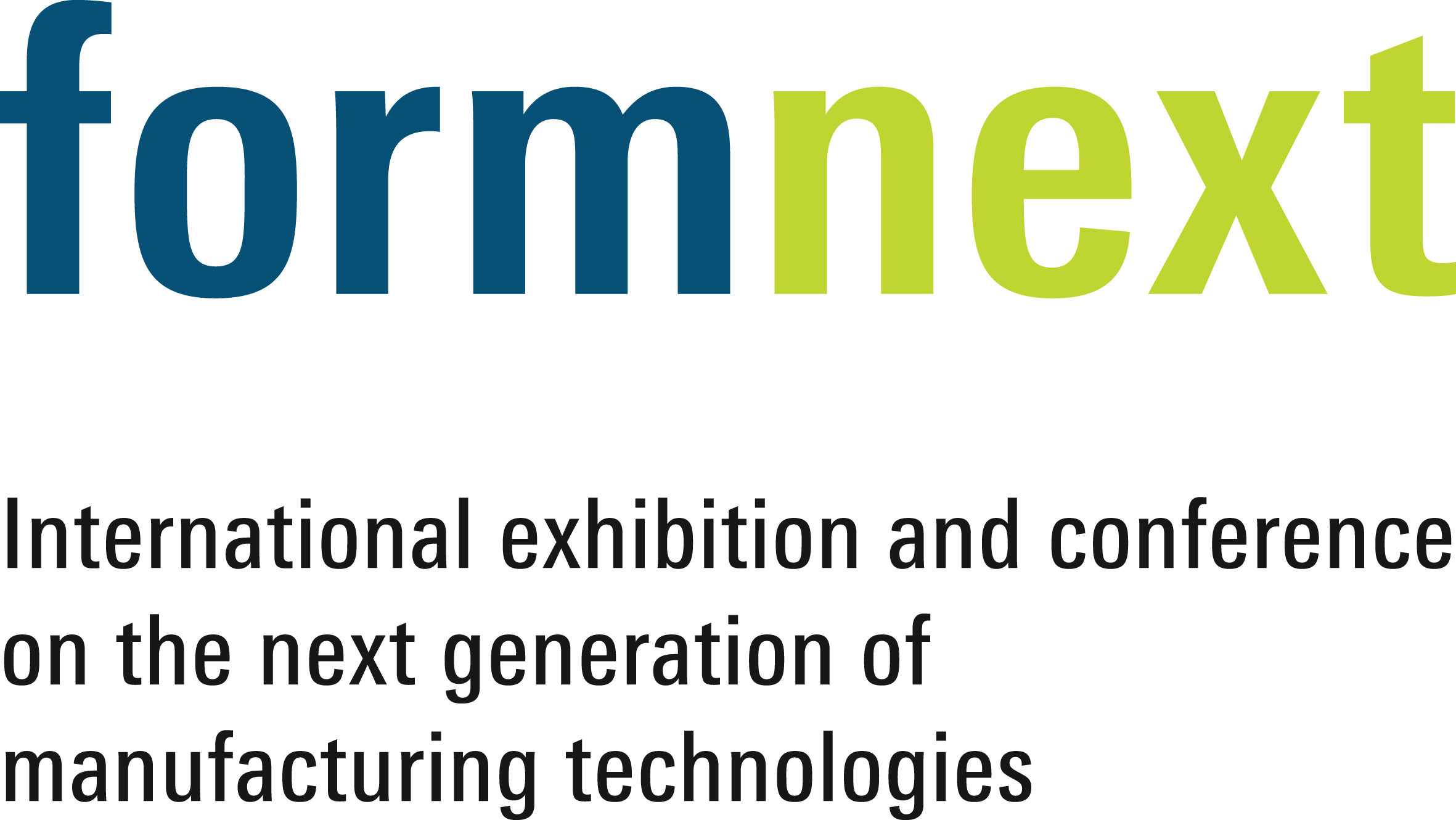
At this year's formnext, we will be presenting groundbreaking innovations in laser technology for additive manufacturing. With our latest developments, we optimise the processing of a wide range of materials, including metals, multimaterials and polymers. As a leading institute in laser research, we will be presenting our state-of-the-art technology, which is specifically tailored to the needs of a wide range of industries. You can look forward to exciting innovative solutions that set new standards. Visit us at the Fraunhofer joint stand in Hall 11 Stand D31 and discover how we are shaping the future of additive manufacturing!
With the generation of complex intensity distributions, we are at the beginning of the revolution in metal additive manufacturing. The scaling of the conventional single beam process is often limited by process instabilities. Available laser power remains unutilised. And the costs for multi-beam processes increase with their productivity. Simple intensity distributions, such as ring-shaped intensity distributions, now show positive effects on the stability of the melt pool and the melt pool geometry. With the advent of high-performance SLM for complex beam shaping, this opens up enormous potential for additive manufacturing
From 2024, European companies will be obliged by the Corporate Sustainability Reporting Directive to provide sustainability information for their production. The LPBF Application Development Group supports customers with Life Cycle Inventory (LCI) studies that analyse material and energy flows in additive manufacturing. Using the latest software tools and a broad database, the group carries out cradle-to-gate analyses to calculate the carbon footprint of components, including the extraction of raw materials.
Ecological assessments are carried out using life cycle assessments (LCA), in which the material and energy flows of various processes, such as the laser powder bed fusion (LPBF) process, are recorded. Primary data is collected at plant level in order to develop process models from the raw material phase through to recycling and to reduce emissions through sustainable alternatives. Analyses show that additive manufacturing, despite its high energy consumption, is ecologically more advantageous than conventional processes, especially for repair applications in the aviation secto
The combination process Simultaneous Machining and Coating (SMaC) developed at the Fraunhofer ILT enables the combination of the EHLA coating process with a subtractive finishing step in parallel with the main production time, thus increasing productivity enormously. In addition to the economic advantages, the SMaC process also offers technological benefits compared to the conventional process chain. The process heat generated in the coating process leads to a softening of the material and thus to easier machining. This makes it possible to produce corrosion and wear protection coatings as well as functional surfaces more quickly and with less wear on the tools. SMaC technology offers considerable advantages, particularly when applying high-strength coating materials that are otherwise difficult to machine.
Besides the requirements for climate protection, the space industry is underlying increasing cost pressure due to international competition. To maintain the European competitiveness, Fraunhofer ILT is part of the ongoing EU project ENLIGHTEN and is developing an additive manufacturing process for rocket nozzles using LMD. The specifications of a rocket nozzle require the productive manufacturing of large components with filigree cooling channels, which is made possible by the LMD technology.
The SLSElasto research project is developing the entire selective laser sintering (SLS) process chain for a novel thermoplastic polyurethane (TPU) powder with a Shore A hardness of 45 to 60, which is significantly lower than the currently available TPU powders with a hardness of 70 to 90. This reduced hardness opens up a wider range of applications and increases the performance and versatility of the SLS technology. The results of the project's investigation could lead to the production of customized, durable and functional components that are valuable in various industries, including healthcare (e.g. orthotics), sports equipment (e.g. airless balls), robotics (e.g. grippers) and the automotive industry (e.g. sealings).
Additive manufacturing opens up a wide range of design options in the production of 3D components, but insufficient surface quality often poses a challenge. High surface roughness impairs the mechanical properties and visual appearance of the components. This is particularly problematic for plastic optics, which require extremely low roughness for sharp images. While injection moulded components usually have a sufficient surface quality, flexible and fast post-processing is required in prototype construction. This is where laser polishing offers efficient solutions for improving surface roughness.
Almost any 2D geometries can be laser polished using the quasi-top-hat scanning strategy. For flat and slightly curved surfaces, there is no need to rotate the component, and surfaces between 1 and 1000 mm² can be polished in a single step, even in hard-to-reach areas. A handling system is used for more complex geometries. Laser polishing significantly reduces the roughness of 3D-printed plastic components. For example, the roughness of an SLS-printed PA12 component is reduced from Sa = 10 μm to Sa = 0.5 μm. For PEEK components produced using the FDM process, the roughness is reduced from Sa = 15 μm to Sa = 0.5 μm. Laser polishing is therefore an effective method for improving surface quality and offers potential for further optimising additive manufacturing, especially for applications with high surface roughness requirements.
In the context of ‘Industry 4.0’, intelligent components that can provide data on their production status and condition are becoming increasingly important. One very promising method for producing such ‘smart parts’ is the combination of thin film processing (TFP) with additive manufacturing. This approach not only allows sensors to be freely positioned in the component, but also to be additively manufactured directly with the component.
The Fraunhofer ILT is developing process chains to integrate sensors such as strain gauges into additively manufactured components. The Laser Powder Bed Fusion (LPBF) process is interrupted during component production in order to manufacture the sensor using TFP technology. The different materials and structures are printed directly onto the component layer by layer and then functionalised (sintered, melted, hardened, etc.) using laser radiation. Once sensor production is complete, the LPBF process is continued in order to fully integrate the sensor into the component.
The result of this process chain is the direct integration of multi-material layer systems into complex components without the need to prepare discrete sensors. This technology offers great potential, particularly for mechanically stressed components in areas such as toolmaking, turbomachinery or combustion engines. Furthermore, the combination of printed electronics and additive manufacturing represents a key technology for the production of intelligent components.