Frankfurt / 19. November 2024 - 22. November 2024
Formnext 2024
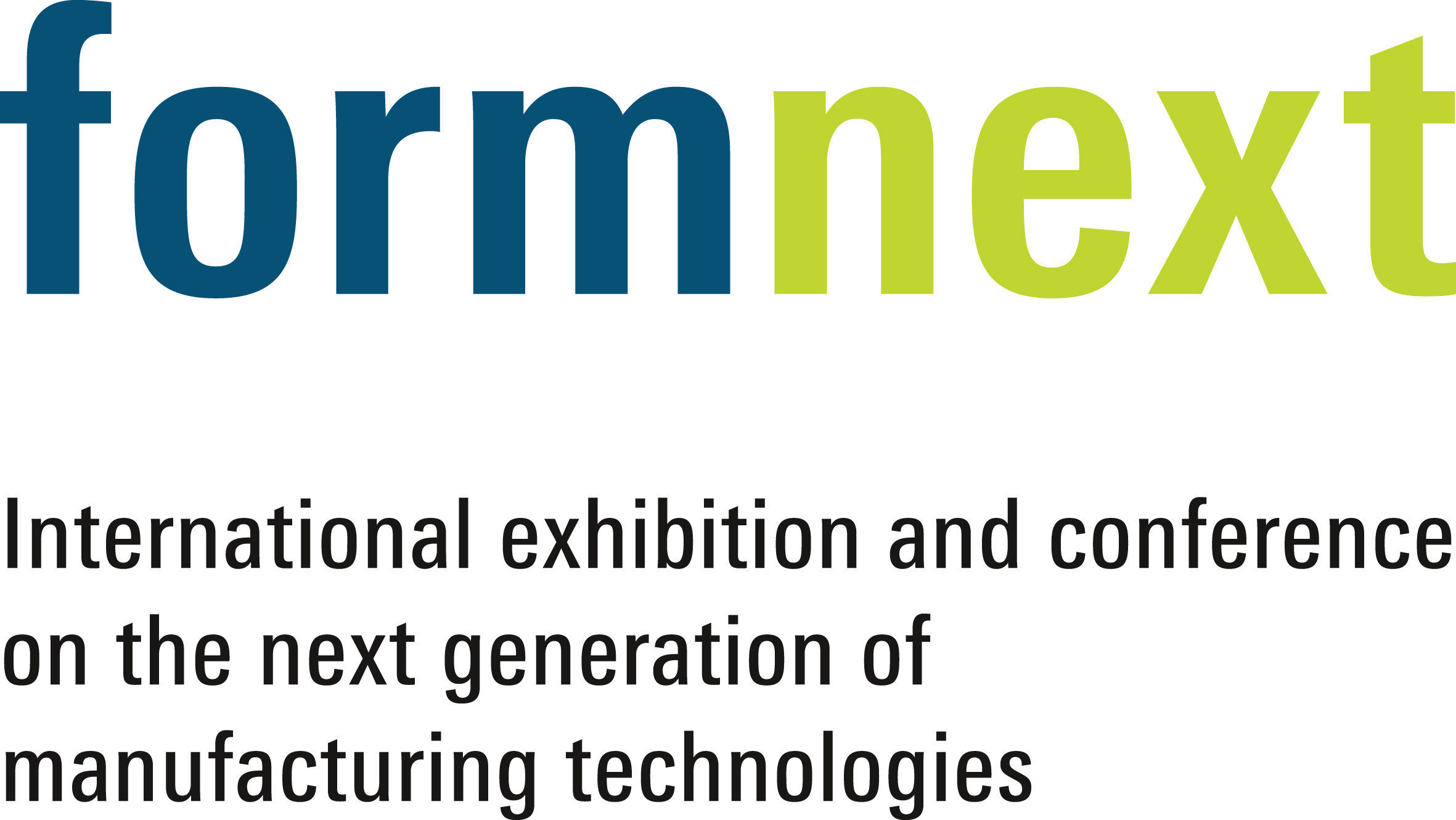
Auf der diesjährigen formnext präsentieren wir Ihnen wegweisende Innovationen aus der Lasertechnologie für die Additive Fertigung. Mit unseren neuesten Entwicklungen optimieren wir die Verarbeitung verschiedenster Materialien, darunter Metalle, Multimaterialien und Kunststoffe. Als führendes Institut in der Laserforschung stellen wir Ihnen unsere neuesten Entwicklungen vor, die gezielt auf die Bedürfnisse unterschiedlichster Branchen zugeschnitten sind. Freuen Sie sich auf spannende Technologien und Lösungen, die neue Maßstäbe setzen. Besuchen Sie uns auf dem Fraunhofer-Gemeinschaftstand in Halle 11 Stand D31 und entdecken Sie, wie wir die Zukunft der additiven Fertigung gestalten!
Mit der Erzeugung von komplexen Intensitätsverteilungen stehen wir am Beginn der Revolutionierung der metallischen additiven Fertigung. Die Skalierung des konventionellen Einzelstrahlprozesses ist oft durch Prozessinstabilitäten eingeschränkt. Zur Verfügung stehende Laserleistung bleibt ungenutzt. Und die Kosten für Multistrahlprozesse skalieren mit deren Produktivität. Simple Intensitätsverteilungen, wie z.B. ringförmige Intensitätsverteilungen, zeigen nun positive Effekte auf die Stabilität des Schmelzbades und die Schmelzbadgeometrie. Mit dem Aufkommen von Hochleistung-SLM zur komplexen Strahlformung wird damit ein enormes Potential für die additive Fertigung eröffnet.
Ab 2024 sind europäische Unternehmen durch die Corporate Sustainability Reporting Directive verpflichtet, Nachhaltigkeitsangaben für ihre Fertigung zu liefern. Die Gruppe LPBF-Applikationsentwicklung unterstützt Kunden dabei mit Life Cycle Inventory (LCI) Studien, die Stoff- und Energieströme in der additiven Fertigung bilanzieren. Mit aktuellen Softwaretools und einer breiten Datenbasis führt die Gruppe Cradle-to-Gate-Analysen durch, um den CO₂-Fußabdruck von Bauteilen zu berechnen, einschließlich der Rohstoffgewinnung.
Ökologische Bewertungen erfolgen über Life Cycle Assessments (LCA), bei denen Stoff- und Energieströme verschiedener Prozesse, wie dem Laser Powder Bed Fusion (LPBF)-Verfahren, erfasst werden. Primärdaten werden auf Anlagenebene erhoben, um Prozessmodelle von der Rohstoffphase bis zum Recycling zu entwickeln und Emissionen durch nachhaltige Alternativen zu reduzieren. Analysen zeigen, dass die additive Fertigung trotz ihres hohen Energieverbrauchs ökologisch vorteilhafter ist als konventionelle Verfahren, insbesondere bei Reparaturanwendungen im Luftfahrtsektor.
Durch das am Fraunhofer ILT entwickelte, Kombinationsverfahren Simultaneous Machining and Coating (SMaC) kann die hauptzeitparallele Kombination des EHLA-Beschichtungsprozess mit einem subtraktiven Fertigbearbeitungsschritt umgesetzt und die Produktivität enorm gesteigert werden. Neben den wirtschaftlichen Vorteilen bietet das SMaC-Verfahren im Vergleich zur konventionellen Prozesskette auch technologische Vorzüge.
Die in dem Beschichtungsvorgang entstehende Prozesswärme führt zu einer Entfestigung des Werkstoffs und damit zu einer einfacheren Zerspanung. Dadurch ist eine werkzeugschonendere und schnellere Herstellung von Korrosions- und Verschleißschutzschichten sowie funktionaler Oberflächen möglich. Insbesondere beim Auftragen andernfalls schwer zerspanbarer, hochfester Beschichtungswerkstoffe ergeben sich durch die SMaC-Technologie erhebliche Vorteile
Neben der politischen Klimaschutzauflagen steht die Raumfahrindustrie aufgrund der internationalen Konkurrenz unter steigendem Kostendruck. Um die europäische Konkurrenzfähigkeit zu erhalten, entwickelt das Fraunhofer ILT im Rahmen des laufenden EU-Projekts ENLIGHTEN einen additiven Fertigungsprozess von Raketendüsen mittels LMD. Die Spezifikationen einer Raketendüse erfordern den produktiven Aufbau eines großen Bauteils mit filigranen Kühlkanälen, die durch die LMD-Technologie ermöglicht wird.
Im Projekt SLSElasto wird die gesamte Prozesskette des Selektiven Lasersinterns (SLS) für ein neuartiges thermoplastisches Polyurethanpulver (TPU) mit einer Shore-A-Härte von 45 – 60 entwickelt, was signifikant niedriger ist als die derzeit verfügbaren TPU-Pulver mit einer Härte von 70 – 90. Diese reduzierte Härte ermöglicht ein breiteres Anwendungsspektrum und steigert die Leistungsfähigkeit sowie Vielseitigkeit der SLS-Technologie. Die Forschungsergebnisse des Projekts könnten zur Herstellung maßgeschneiderter, langlebiger und funktionaler Komponenten führen, die in verschiedenen Branchen von Vorteil sind, darunter Medizintechnik (z. B. Orthesen), Sportartikel (z. B. luftfreie Bälle), Automatisierungstechnik (z. B. Greifer) und die Automobilindustrie (z. B. Dichtungen).
Die additive Fertigung eröffnet vielfältige Gestaltungsmöglichkeiten bei der Herstellung von 3D-Bauteilen, doch die unzureichende Oberflächenqualität stellt oft eine Herausforderung dar. Eine hohe Oberflächenrauheit beeinträchtigt die mechanischen Eigenschaften und das optische Erscheinungsbild der Bauteile. Besonders bei Kunststoffoptiken, die eine extrem geringe Rauheit für scharfe Abbildungen erfordern, ist dies problematisch. Während Spritzgussbauteile meist eine ausreichende Oberflächenqualität aufweisen, ist im Prototypenbau eine flexible und schnelle Nachbearbeitung erforderlich. Hier bietet das Laserpolieren effiziente Lösungen zur Verbesserung der Oberflächenrauheit.
Mithilfe der Quasi-Top-Hat-Scanstrategie lassen sich nahezu beliebige 2D-Geometrien laserpolieren. Bei planen und leicht gekrümmten Oberflächen entfällt die Rotation des Bauteils, und Flächen zwischen 1 und 1000 mm² können in einem Schritt poliert werden, auch an schwer zugänglichen Stellen. Für komplexere Geometrien wird ein Handlingsystem eingesetzt. Das Laserpolieren reduziert die Rauheit von 3D-gedruckten Kunststoffbauteilen deutlich. Beispielsweise wird die Rauheit eines SLS-gedruckten PA12-Bauteils von Sa = 10 μm auf Sa = 0,5 μm reduziert. Bei PEEK-Bauteilen, die im FDM-Verfahren hergestellt werden, sinkt die Rauheit von Sa = 15 μm auf Sa = 0,5 μm. Das Laserpolieren stellt somit eine effektive Methode zur Verbesserung der Oberflächenqualität dar und bietet Potenzial, die additive Fertigung weiter zu optimieren, insbesondere bei Anwendungen mit hohen Anforderungen an die Oberflächenrauheit.
Im Kontext von "Industrie 4.0" gewinnen intelligente Bauteile, die Daten über ihren Produktionsstatus und Zustand liefern können, zunehmend an Bedeutung. Eine vielversprechende Methode zur Herstellung solcher „smart parts“ ist die Kombination von Thin Film Processing (TFP) mit additiver Fertigung. Durch diesen Ansatz können Sensoren nicht nur frei im Bauteil positioniert, sondern auch direkt mit dem Bauteil additiv gefertigt werden.
Das Fraunhofer ILT entwickelt Prozessketten, um Sensoren wie Dehnungsmessstreifen in additiv gefertigte Bauteile zu integrieren. Der Laser Powder Bed Fusion (LPBF)-Prozess wird während der Bauteilherstellung unterbrochen, um den Sensor mithilfe der TFP-Technologie zu fertigen. Die unterschiedlichen Materialien und Strukturen werden dabei Schicht für Schicht direkt auf das Bauteil aufgedruckt und anschließend mittels Laserstrahlung funktionalisiert (gesintert, geschmolzen, gehärtet etc.). Nach Abschluss der Sensorfertigung wird der LPBF-Prozess fortgeführt, um den Sensor vollständig in das Bauteil zu integrieren.
Das Ergebnis dieser Prozesskette ist die direkte Integration von Multimaterialschichtsystemen in komplexe Bauteile, ohne dass diskrete Sensoren vorbereitet werden müssen. Diese Technologie bietet insbesondere für mechanisch belastete Bauteile in Bereichen wie Werkzeugbau, Turbomaschinen oder Verbrennungsmotoren großes Potenzial. Darüber hinaus stellt die Kombination aus „printed electronics“ und additiver Fertigung eine Schlüsseltechnologie für die Herstellung intelligenter Bauteile dar.