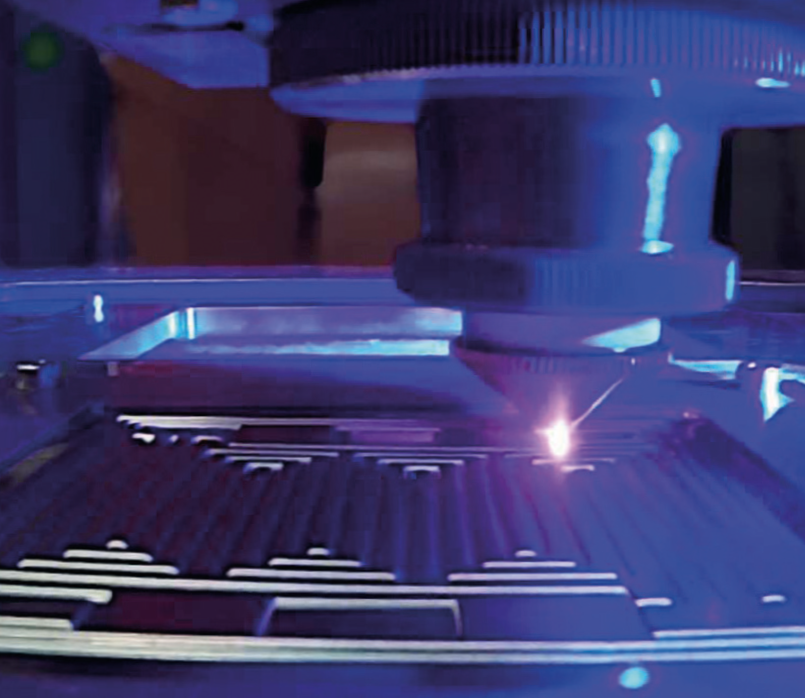
Grüner Wasserstoff ist der Energieträger der Zukunft. Zu den potentiellen Anwendungsgebieten zählen die Mobilität sowie die Hausenergieversorgung auf Brennstoffzellenbasis. Für eine breite Marktdurchdringung bedarf es neben technologischen Weiterentwicklungen vor allem einer deutlichen Kostenreduktion entlang der Wertschöpfungsketten von Elektrolyseuren, Brennstoffzellen und deren Komponenten. Hochproduktive Laserverfahren spielen bei der Skalierung der Herstellungsprozesse eine entscheidende Rolle.