Frankfurt a. M. / 19. November 2019 - 22. November 2019
formnext
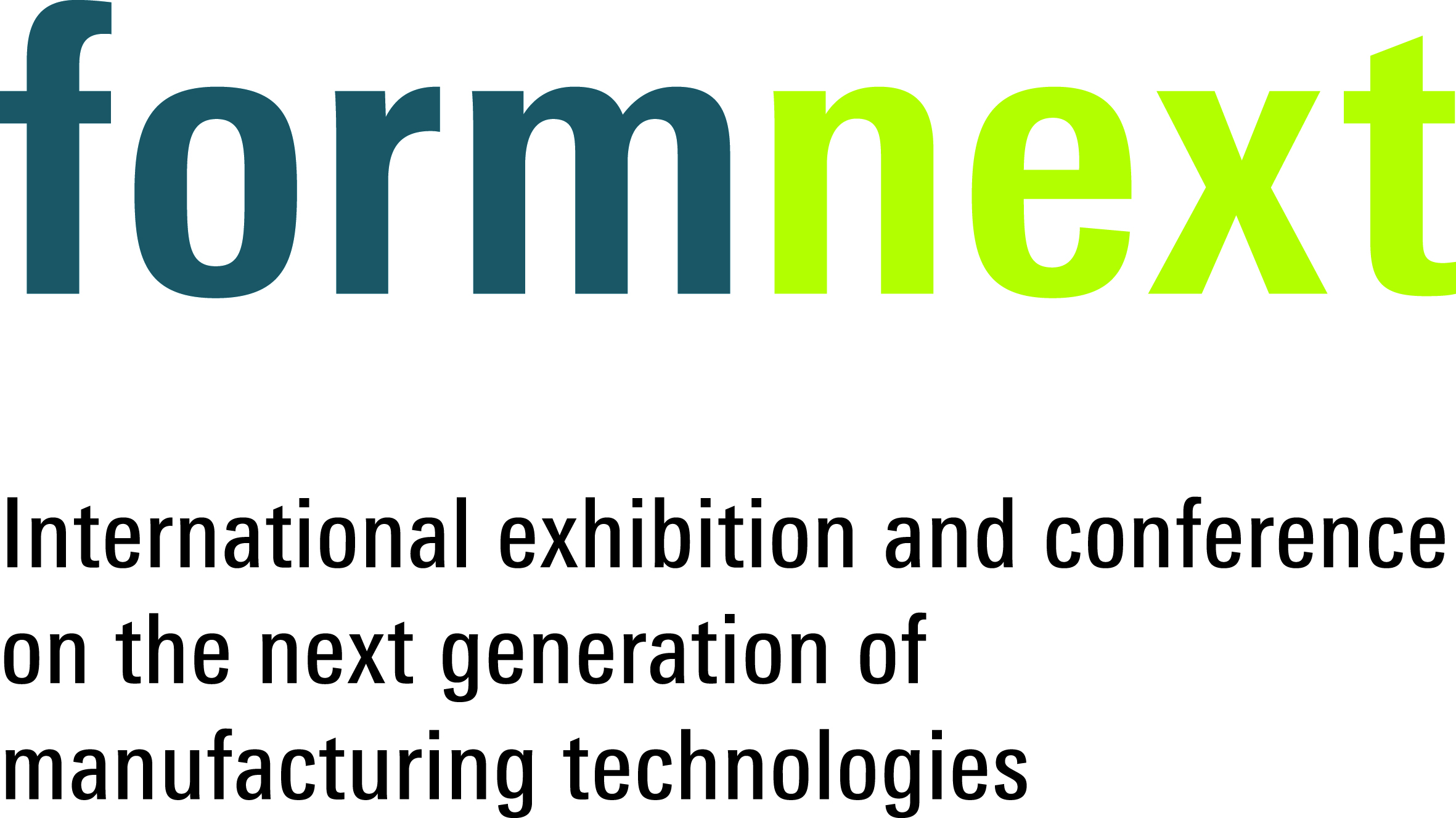
Beim Laser Powder Bed Fusion (LPBF) werden Bauteile Schicht für Schicht mit dem Laser aus dem Pulverbett aufgebaut. Durch Temperaturunterschiede im Bauteil entstehen dabei mechanische Spannungen. Je nach Geometrie und Werkstoff kann das sogar zur Rissbildung führen.
Mit Partnern aus der Industrie haben Experten vom Fraunhofer-Institut für Lasertechnik ILT deshalb Ideen umgesetzt, bei denen das Bauteil von oben erwärmt wird. Schon 2018 wurden dafür im Rahmen des Forschungscampus Digital Photonic Production DPP an der RWTH Aachen vertikal emittierende Laserbarren (VCSEL) präsentiert, die mit je 1 kW Leistung von oben in die Kammer strahlen.
Jetzt hat das Team mit dem Partner adphos GmbH eine Lösung entwickelt, bei der ein Nahinfrarot (NIR)-Strahler an der Rakel befestigt ist und mit seiner breitbandigen Strahlung das Material in der Prozessebene erwärmt.
Mit bis zu 12 kW Leistung schafft der NIR-Strahler Temperaturen von 500 bis über 800 Grad im Bauteil. Die NIR-Beleuchtung ist räumlich homogen und lässt sich sehr gut skalieren.
Hochreines Kupfer ist wegen seiner elektrischen Leitfähigkeit besonders bei stromführenden Komponenten und im Wärmemanagement gefragt und spielt somit u.a. eine wichtige Rolle in der Elektrotechnik, dem Maschinenbau und der Elektromobilität.
Der metallische 3D-Druck mit hochreinem Kupfer mittels Laser Powder Bed Fusion (LPBF) und infrarotem Licht ist bislang nur schwierig umzusetzen, da geringe Aufbauraten und eine inhomogene Bauteilqualität durch einen instabilen Umschmelzprozess für den Anwender nicht zufriedenstellend sind.
Diese Problematik wird nun durch den Einsatz einer neuen Laserstrahlquelle im grünen Spektralbereich gelöst. Bauteile aus hochreinem Kupfer konnten erstmals mit einer relativen Materialdichte von mehr als 99,8 % und einer Leitfähigkeit von 58 MS/m aufgebaut werden.
Das Fraunhofer ILT untersucht den Einfluss grüner sowie blauer Wellenlängen auf die pulverbettbasierte Additive Fertigung. Im Mittelpunkt stehen dabei hoch reflektive Materialien wie Kupfer und seine Legierungen. Untersucht wird zudem, ob sich mit grünem und blauem Laserlicht die Prozessqualität, Produktivität und Effizienz für die Additive Fertigung von etablierten Werkstoffen im metallischen 3D- Druck steigern lassen.
Im Rahmen des durch das Bundesministerium für Bildung und Forschung (BMBF/KIT) geförderten Projekts ProLMD entwickeln das Fraunhofer ILT und industrielle Partner neue Prozesse, um hybride LMD-Verfahren in die Fertigungskette zu integrieren. Entstehen sollen Verfahren und Anlagen, mit denen sich beispielsweise Verstärkungen oder andere Geometrieelemente auf Guss- oder Schmiedeteile mit Hilfe von LMD auftragen lassen.
Eine wichtige Rolle spielt eine neue Bearbeitungsoptik zum koaxialen Laserauftragschweißen (LMD) mit Draht und einem Ringstrahl, die innerhalb des ProLMD-Verbundprojektes entstand.
Für die neue Bearbeitungsoptik sprechen vor allem die Richtungsunabhängigkeit sowie die gleichmäßige Intensitätsverteilung des Laserstrahlrings. Es sind hohe Leistungen bis 4 kW dank des Einsatzes von reflektiven Optiken (Kupfer) für einen großen Wellenlängenbereich nutzbar. Es lassen sich daher auch große Bauteile in einer sehr hohen Qualität ohne Poren und sehr wenig Nachbearbeitung herstellen. Außerdem ermöglicht der neue Kopf das Schweißen auf 3D-Flächen. Wie bei den meisten LMD-Verfahren eignet sich die neue Optik aber auch zur Reparatur von Bauteilen.
Laserauftragschweißen (LMD) hat sich beim Auftragen von Schutzschichten, der Reparatur von hochwertigen Bauteilen sowie beim metallischen Additive Manufacturing bewährt. Die Qualität einer Beschichtung nach dem LMD-Verfahren steht und fällt u.a. mit den Laser-Kennwerten, der Pulverzuführung, dem Vorschub, der Beschaffenheit des Werkstücks und dem Schutzgas.
Abweichungen lassen sich am besten am Pulvergasstrahl ablesen. Bisher fehlten jedoch prozessichere Überwachungsverfahren dazu.
Das vom Fraunhofer ILT entwickelte standardisierte Verfahren »Powder Jet Monitor (PJM)« ermöglicht, dass sich Pulverdüsen für einen LMD-Prozess zertifizieren lassen. Die Anlagentechnik eignet sich zur Messung außerhalb des Laserauftragschweißens, kann jedoch auch zur Offline-Messung in eine LMD-Anlage integriert werden. Wann und wie oft der Anwender die Messung durchführt ist von der jeweiligen Applikation abhängig.
Das Verfahren wird bereits verwendet um das Extreme Hochgeschwindigkeits-Laserauftragschweißen (EHLA) weiter zu optimieren.
Mit dem Fraunhofer-Leitprojekt futureAM treibt die Fraunhofer-Gesellschaft die Weiterentwicklung der additiven Fertigung metallischer Bauteile systematisch voran. Dazu sind sechs erfahrene Fraunhofer-Institute im Bereich Additive Fertigung eine strategische Projektpartnerschaft eingegangen und haben sich zwei wesentliche Ziele gesetzt:
1. den Aufbau einer übergreifenden Kooperationsplattform für die hochintegrative Zusammenarbeit und die Nutzung der dezentral verteilten Ressourcen der Fraunhofer-Gesellschaft im Bereich Additive Manufacturing (AM)
2. die Schaffung der technologischen Voraussetzungen für eine praxisrelevante Steigerung von Skalierbarkeit, Produktivität und Qualität von AM-Prozessen für die Fertigung individualisierter Metallbauteile
Beispiele für die ambitionierten Projektziele sind:
eine neuartige Software zur automatisierten AM-Bauteilidentifikation und -optimierung
ein skalierbares LPBF-Anlagenkonzept mit Produktivitätssteigerung (Faktor > 10)
ein Verfahren sowie eine Systemtechnik zur Erzeugung ortsaufgelöster, maßgeschneiderter Multi-Materialeigenschaften
eine autonome Fertigungszelle für die Nachbehandlung von AM-Bauteilen
Die Kooperationsplattform wird nicht nur durch die intensive Zusammenarbeit in und zwischen den einzelnen Handlungsfeldern geschaffen, sondern insbesondere durch den Aufbau eines »Virtual Lab«. Aus diesem heraus werden unter Beteiligung aller Partner Technologie-Demonstratoren entwickelt.